Made In England
The surroundings might be entirely unassuming – a stretch of industrial park on the outskirts of Gloucestershire – but once within, a thriving hive of activity unfolds.
This is Turnbull & Asser’s shirting factory – a series of buildings where every aspect of a shirt’s anatomy is produced. The traditional ideal of an artisanal shirting outfit might conjure up romantic images of thimbles, thread and quiet industry by the fireside, but the reality – despite the green rolling hills of the Cotswolds in the distance – is somewhat more strikingly modern; workstations are neatly positioned around the workshop, machines whirl and paper sketches of shirt templates inform the designs.
‘Lots of companies have machine operatives, and a lot of manufacturing is automated,’ says Kathleen Cope, who alongside her twin sister Bette Elton has been with the company for an astonishing 54 years, having started on the same day aged 15. ‘Turnbull & Asser prides itself on not being automated. We have machinists here, not machine operatives. Each person has a particular skill and we work on their strengths, but each one of them can also produce a shirt all the way through. It’s that human skill that’s so important.’
It’s certainly been an ethos of Turnbull & Asser since it began life in 1885 in London’s St James’s – a historic mecca for menswear in the capital – creating shirts for the considered elite, before branching into accessories and clothes. It’s particularly fitting that the house has adhered to a stringent ‘Made in England’ ethos; there is a style that’s distinctly and unwaveringly British, from the swirling paisley print and club stripe ties that recall the rowing elite of Oxford and Cambridge, to the icons that have helped cement the brand in the public consciousness.

Sir Winston Churchill led Britain through the Second World War in his Turnbull & Asser “siren suit”, HRH Prince Charles is a devotee (as are his sons), and the brand has created shirts for arguably Britain’s biggest cinematic export, James Bond, since Sean Connery slipped on a dinner jacket for the role. ‘We certainly like seeing the shirts on screen,’ says Cope on making the shirts for Daniel Craig as the latest Bond, ‘particularly in the underwater or action scenes – I watch and think “those seams have held up well there”.’ A wander through the hallowed halls of the Turnbull & Asser workrooms reveals portraits of HRH the Prince of Wales visiting the factory, alongside the great and the good of Hollywood. And it stands to reason that those seams hold up so well under pressure; the shirts produced here – both ready-to-wear and bespoke – are made to the most exacting standards, each handcrafted by individuals who have been with the company for, in some cases, several decades.
The story starts with the patterns that arrive in the pattern-cutting room, a cavernous space where fabrics spill from boxes and rolls of materials – from fresh white cotton to discreetly shaded plaids and windowpane checks – sit awaiting their turn on the cutting tables. Patterns arrive and are transported to the cutters, who nip, snip and finetune the shapes, measuring with the exactness of surgeons. Bespoke shirts require extra care to get the exactitude of someone’s particular measurements just right. From here, the shirts go to the sewing room to be painstakingly pieced together and have the fi ne details – cuffs, collars, buttons, seams, darts and pockets – laboured over. The process, while demanding, and requiring years of training, is a streamlined one, at least for the ready-to-wear shirting. Each one takes around 40 minutes to craft by hand once it arrives here. ‘The most time consuming elements are things like the collar, it’s the selling point of the shirt, and then the cuffs. Every single element is important but the collar has to be perfection,’ says Cope.
Each craftsperson works on one individual element, from pressing collar peaks into a heated press to seal part of them, to sewing on the mother-of-pearl buttons – before passing down the bustling production line, each workstation dotted with a Union Jack flag fluttering merrily, a nod to this most British of institutions, while a rainbow arrangement of thread spools, uniform in their plastic boxes, look on.
The bespoke set-up, whereby a customer can request any myriad adjustments to the design and make-up of the shirt, is slightly different – initials may have to be stitched into cuffs, contrasting trims might be required on collars or in the case of a recent woman’s shirt that came through the factory, a curved pyjama collar might be specially asked for. ‘If we haven’t done something before, we simply work on finding a way to do it and invent new ways. It’s all about what the customer wants and it’s our job to make it happen.’
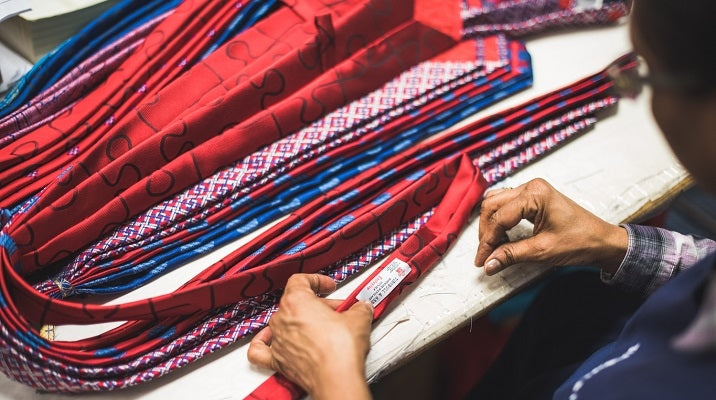
It’s a similar story at Turnbull & Asser’s tie factory in Kent, which is proud of its place in UK manufacturing; the residential street and office blocks bely the sartorial history beyond its doors (although the move here is a recent one; it was previously based in Waterloo). The starting point here are the fabrics which arrive from British mills; Turnbull & Asser is known for the vibrancy of its accessories, with its ties and bow ties coming in many patterns and colours. From here, the orders are run through – overseen by office supervisor Victoria Redondo – and cutters begin work on the cutting process, as within the shirting factory, to distinct lines of the tie-blade, gusset – the piece that joins the shorter end of the tie to the larger end – the underend, and tip lining. From here, one of the machinists will begin to work on the various elements, which is where a high degree of dexterity and skill comes into play.
To ensure strength and durability within the structure of the tie, the slip-stitch acts as the veritable backbone of the accessory; a stitch that sits behind the blade and acts as a backbone down its middle. It ends with a special ‘loop’ at the narrow end of the tie which allows the stitch to, in effect, ‘slip’ slightly; what this means in reality is that it can be ruched and then flattened back smoothly, to be able to stand up to daily rigours and still look impeccable (we’re looking at you, Mr Bond).
Like Turnbull & Asser’s shirting factory, the process is swift and streamlined – one ready-to-wear tie will take 30 minutes, bespoke can be as quick as 48 hours from the design leaving the shop in St James’s to returning – and its craftspeople have been here for decades; the longest serving member is a pattern cutter who worked there for 20 years.
In a climate of mass production and fast fashion, it’s this family-centric, intergenerational approach that lies at the heart of the house’s Made-in-England ethos. ‘My son works in the factory, alongside my sister,’ says Cope, who points out that various other families have more than one member working within the company.
And at a time when traditional British craft is in decline, Turnbull & Asser is dedicated to training the younger generation and supporting an entire industry devoted to Made-in-Britain excellence, from umbrellas from Fox Brothers in Somerset, to cashmere from Begg & Co in Scotland. So the next time you’re adjusting your bow tie or buttoning your shirt, you can rest assured that a very British spirit and sense of expertise, has gone into every stitch.